Reports of Chinese copies of the ELM327 not actually implementing the SAE J1850 VPW protocol can be readily found. Some have opened up their adapters to find pin 2 of the OBD connector not even connected. Here I use a serial terminal to test the output of an ELM327 copy for presence of a voltage output on pin 2 during a simple J1850 message. I have set the ELM to use protocol #2, SAE J1850 VPW, and I have a multimeter attached to ground and pin #2 of the OBD adapter. The meter is set to 2000 millivolts DC. The voltage can be seen to increase during the sending of the message.
This same operation can be duplicated in the vehicle by removing the sp205 comb and connecting the voltmeter to terminal A (purple wire) and a known good ground. The purple wire from the DLC and sp205 should be tested for continuity as well as no shorts to ground or power first.
While this does not prove operability of the ELM327 copy it at least proves there is some connection internally and at the least suggests the device supports the J1850 protocol.
Here are 2 stills from the video with the voltmeter showing the increased voltage during message transmission.
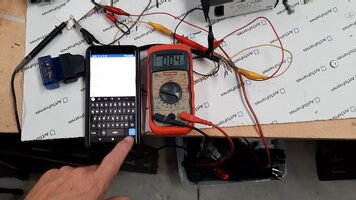
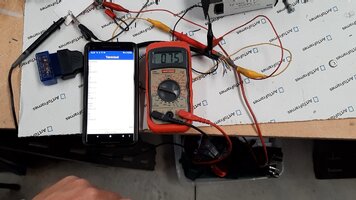
This same operation can be duplicated in the vehicle by removing the sp205 comb and connecting the voltmeter to terminal A (purple wire) and a known good ground. The purple wire from the DLC and sp205 should be tested for continuity as well as no shorts to ground or power first.
While this does not prove operability of the ELM327 copy it at least proves there is some connection internally and at the least suggests the device supports the J1850 protocol.
Here are 2 stills from the video with the voltmeter showing the increased voltage during message transmission.
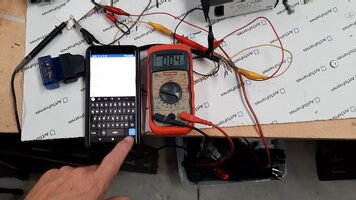
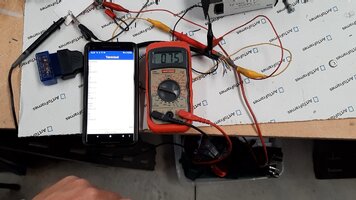