Yes... The MOST Positive Rust Prevention possible is by protecting Bare Mild Steel and Cast Iron using a Passive Zinc Metal Etching when treating those surfaces using THIS Strong Zinc-Acid Metal Etching Liquid called POR-15 "Metal Prep"...when VERY carefully applied with a cut-down Turkey Basting Brush.
Likewise ...the Bare Metal must first be washed off using the Special POR-15 De-Greasing Detergent via a Sponge and then later washing it away using Warm Water and hand drying using Scott "Blue" Shop Towels or hitting it lightly with a Blow Drier to avoid rapid rusting in the air.
Then immediately afterwards, for around 30-45 Minutes, apply the Wet Brushing of this Acid so as to deposit a Thin, Durable, Bonded Zinc Coating in place of the Normal Oxidation that occurs when Iron combines with Oxygen to form FE203 (RED RUST).
It is important to keep the Surfaces being so treated very "WET" the entire time when applying the "Metal Prep" Liquid throughout this procedure to ensure a Chemical Zinc "Etching Chemistry" Transfer.

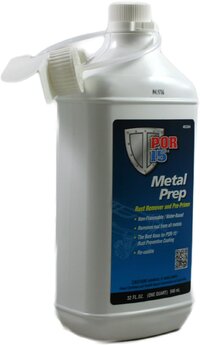
Once the Mild Steel is thusly Chemically "RUSTED" ...it will NOT degrade...and in fact this process will also allow for the item to be likewise Very Carefully Painted with POR-15 Black, Hard Paint via THIS Kit which has All Three Components along with the Bristle Brush, paint Applicator and Rubber Gloves necessary for this Complete Job. THIS is a much more economical approach to the work, since "A VERY Little POR-15 ... Goes a VERY Long Way... " Of course, every last vestige of the "Metal Prep" Acid must be carefully washed off of the Metal areas and then dried prior to being painted with POR-15.
As you know... ordinary Paint will NOT stick to these unprepared Ferrous - Iron Surfaces: There are MANY On Topic YT Videos showing all of these procedures on various projects, both large and small... along with the Caution and Warning NOT to get this Paint on Human Skin as once it dries... must WEAR off over time in order to remove it
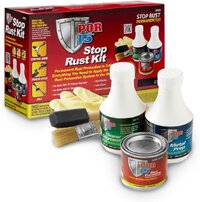
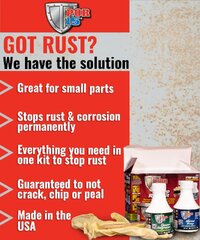

Likewise ...the Bare Metal must first be washed off using the Special POR-15 De-Greasing Detergent via a Sponge and then later washing it away using Warm Water and hand drying using Scott "Blue" Shop Towels or hitting it lightly with a Blow Drier to avoid rapid rusting in the air.
Then immediately afterwards, for around 30-45 Minutes, apply the Wet Brushing of this Acid so as to deposit a Thin, Durable, Bonded Zinc Coating in place of the Normal Oxidation that occurs when Iron combines with Oxygen to form FE203 (RED RUST).
It is important to keep the Surfaces being so treated very "WET" the entire time when applying the "Metal Prep" Liquid throughout this procedure to ensure a Chemical Zinc "Etching Chemistry" Transfer.

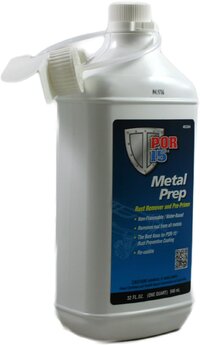
Once the Mild Steel is thusly Chemically "RUSTED" ...it will NOT degrade...and in fact this process will also allow for the item to be likewise Very Carefully Painted with POR-15 Black, Hard Paint via THIS Kit which has All Three Components along with the Bristle Brush, paint Applicator and Rubber Gloves necessary for this Complete Job. THIS is a much more economical approach to the work, since "A VERY Little POR-15 ... Goes a VERY Long Way... " Of course, every last vestige of the "Metal Prep" Acid must be carefully washed off of the Metal areas and then dried prior to being painted with POR-15.
As you know... ordinary Paint will NOT stick to these unprepared Ferrous - Iron Surfaces: There are MANY On Topic YT Videos showing all of these procedures on various projects, both large and small... along with the Caution and Warning NOT to get this Paint on Human Skin as once it dries... must WEAR off over time in order to remove it
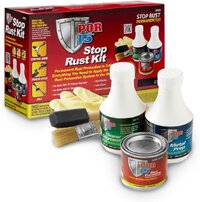
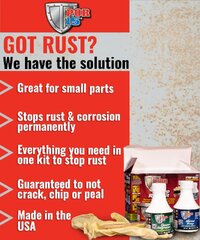

Last edited: