All Right… I've had a chance to catch some much needed 40 Winks of sleep and rested long enough to get the swelling to go down in The Ol’ Left Leg… and so here comes Part Two of the Design, Pre-Fitting and Building of the Framing for “The Franken-Oiler Machine”:
I’ve added some additional images that better capture the appearance of the features I was counting on the Aluminum Racing Fuel Cell to have and I was not disappointed in the least with what I found. When the unit arrived… I checked it over and found inconsequential damage to it in the form of a few of the four soft Aluminum Mounting Tangs that were bent a little bit… but nothing such that it compromised the integrity of the Main Container. This may explain why I was able to get it at such a low price with free S&H. No Problem. And just as I suspected… Dwelling deep inside the inner hollow cavity was a Thick, Strong Black Piece of High Tech, Fuel Resistant Cellular Foam in the dimensions of 2.5” X 11” X 11”.
THIS Sh*t... is some Very Tough Stuff!
The Foam Plank was lodged in the bottom of the tank and hanging on inside like an Alabama Tick… well out of the reach of my fingers and most other common Pliers-Type Tools, And so I resorted to my redoubtable $2.00 Harbour-Freight Extra Long Stainless Steel Haemostat… and using much more force to extract it than you might imagine necessary, I gradually coaxed that Damned Difficult Thing up and out through the Filler Neck.
I was surprised at how incredibly resistant to tearing this stuff was… but I suspect it was placed in there to assist in the reduction of “Fuel Slosh” and to eliminate any chance that any Racing Fuel would accidentally mix with any Fuel Vapours and bubble along with the outflow stream via the two Out-Flow Connectors welded into the lowest areas of the tank bottom and cause fuel starvation in a Racing Engine. But it certainly has no place being in there NOW and would have been a serious impediment to the Flow of Oil coming out of a Filled Tank.
Nonetheless...THIS Container serves all of our purposes to a “T” and is the very thing we need in this case because once vacated of the Foam Plank, you can see very “Well” down inside the entire tank for inspection and cleaning prior to use. If you take notice from the images how the lower tank is bevelled down via a nice sloping angle, you can see that this will guarantee almost every single drop of either Cleaning Solution or Oil fluids can drain out of the tank completely and this serves our purposes very well for the Gravity Feed output of Engine Break-In Lubrication into the 12 Volt Electric Oil Pump.
I wanted to mention a Safety Issue concerning an artefact of using the 7” Harbour Freight Chop Saw- Angle Grinder that you will have to be aware of if you are using it for cutting Angle Iron. Ordinarily... when using either a Fine Tooth Hack-Saw or similar File Type Metal Cutting Tool… the particulate residue from these “partings” would be as fine as Beach Sand and represent no immediate danger; unless exposed to a Pure Oxygen environment where the Fine Iron Filings could spontaneously combust into a violent hot flame... You can actually see a dramatic demonstration of this happening at 25:20 onwards during this video:
But in this instance… the HF Chop Saw creates “Little Razor Blades” along the margins of every cut that are substantially large, strong and capable enough to slice swiftly through your fingers to the bone and could very easily sever skin, tendons and nerves there like they were nothing. I took a few images of these items so you will know what to watch out for and remove them to the trash before being tempted to run your hands and fingers over the freshly sawed edges of each piece of Angle Iron.
The previous entry covers the day’s efforts as far as how to quickly and efficiently Measure, Align, Cut and Drill each pairing and meeting points for the Framing Pieces to make your life easier… and trust me on this...the very last thing you want to have to do is try to prepare Angle Iron Segments to work well enough to guarantee that “ ...everything is Quite Correct” and plumb when finally assembled. This is quite simply impossible to accomplish when the pieces are randomly drilled without being deliberately associated one to the other when laying on the driveway!
First...Square the pieces as sub-assembly groups using the Carpenter's Square while arranging the Work Pieces around for convenience on top of the edges of the Portable Work Table and fix their positions with the Carpentry Clamps to hold everything in place during the cutting and drilling phases. Next...Do the Fitting and Fastening of them together at Pure Right Angles starting with the Left and Right Upright Support Segments is Half the Battle. Then its just a matter of creating sections with lengths of the proper width for the Rectangular Shelving Supports that can easily be added, once you determine how deep they will need to be and how many shelves you require for The Stand.
Earlier this evening… the two Valve Roller Rockers and the Kent-Moore EN-47945 Valve Spring Compressor Tool arrived...(see the attached imagery)… and as soon as the single Valve Lash Adjuster I ordered does too, I’ll attend to swapping out those components at the position between Cylinders 4 & 5 of the Intake Camshaft “Problem Lobe”. It has been a good and productive day...moving things closer and closer to the Engine Install Date. “The FrankenOiler Machine” will go a long way towards making this happen successfully.
More to Follow...
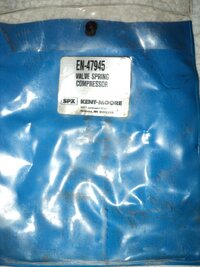
I’ve added some additional images that better capture the appearance of the features I was counting on the Aluminum Racing Fuel Cell to have and I was not disappointed in the least with what I found. When the unit arrived… I checked it over and found inconsequential damage to it in the form of a few of the four soft Aluminum Mounting Tangs that were bent a little bit… but nothing such that it compromised the integrity of the Main Container. This may explain why I was able to get it at such a low price with free S&H. No Problem. And just as I suspected… Dwelling deep inside the inner hollow cavity was a Thick, Strong Black Piece of High Tech, Fuel Resistant Cellular Foam in the dimensions of 2.5” X 11” X 11”.
THIS Sh*t... is some Very Tough Stuff!
The Foam Plank was lodged in the bottom of the tank and hanging on inside like an Alabama Tick… well out of the reach of my fingers and most other common Pliers-Type Tools, And so I resorted to my redoubtable $2.00 Harbour-Freight Extra Long Stainless Steel Haemostat… and using much more force to extract it than you might imagine necessary, I gradually coaxed that Damned Difficult Thing up and out through the Filler Neck.
I was surprised at how incredibly resistant to tearing this stuff was… but I suspect it was placed in there to assist in the reduction of “Fuel Slosh” and to eliminate any chance that any Racing Fuel would accidentally mix with any Fuel Vapours and bubble along with the outflow stream via the two Out-Flow Connectors welded into the lowest areas of the tank bottom and cause fuel starvation in a Racing Engine. But it certainly has no place being in there NOW and would have been a serious impediment to the Flow of Oil coming out of a Filled Tank.
Nonetheless...THIS Container serves all of our purposes to a “T” and is the very thing we need in this case because once vacated of the Foam Plank, you can see very “Well” down inside the entire tank for inspection and cleaning prior to use. If you take notice from the images how the lower tank is bevelled down via a nice sloping angle, you can see that this will guarantee almost every single drop of either Cleaning Solution or Oil fluids can drain out of the tank completely and this serves our purposes very well for the Gravity Feed output of Engine Break-In Lubrication into the 12 Volt Electric Oil Pump.
I wanted to mention a Safety Issue concerning an artefact of using the 7” Harbour Freight Chop Saw- Angle Grinder that you will have to be aware of if you are using it for cutting Angle Iron. Ordinarily... when using either a Fine Tooth Hack-Saw or similar File Type Metal Cutting Tool… the particulate residue from these “partings” would be as fine as Beach Sand and represent no immediate danger; unless exposed to a Pure Oxygen environment where the Fine Iron Filings could spontaneously combust into a violent hot flame... You can actually see a dramatic demonstration of this happening at 25:20 onwards during this video:
But in this instance… the HF Chop Saw creates “Little Razor Blades” along the margins of every cut that are substantially large, strong and capable enough to slice swiftly through your fingers to the bone and could very easily sever skin, tendons and nerves there like they were nothing. I took a few images of these items so you will know what to watch out for and remove them to the trash before being tempted to run your hands and fingers over the freshly sawed edges of each piece of Angle Iron.
The previous entry covers the day’s efforts as far as how to quickly and efficiently Measure, Align, Cut and Drill each pairing and meeting points for the Framing Pieces to make your life easier… and trust me on this...the very last thing you want to have to do is try to prepare Angle Iron Segments to work well enough to guarantee that “ ...everything is Quite Correct” and plumb when finally assembled. This is quite simply impossible to accomplish when the pieces are randomly drilled without being deliberately associated one to the other when laying on the driveway!
First...Square the pieces as sub-assembly groups using the Carpenter's Square while arranging the Work Pieces around for convenience on top of the edges of the Portable Work Table and fix their positions with the Carpentry Clamps to hold everything in place during the cutting and drilling phases. Next...Do the Fitting and Fastening of them together at Pure Right Angles starting with the Left and Right Upright Support Segments is Half the Battle. Then its just a matter of creating sections with lengths of the proper width for the Rectangular Shelving Supports that can easily be added, once you determine how deep they will need to be and how many shelves you require for The Stand.
Earlier this evening… the two Valve Roller Rockers and the Kent-Moore EN-47945 Valve Spring Compressor Tool arrived...(see the attached imagery)… and as soon as the single Valve Lash Adjuster I ordered does too, I’ll attend to swapping out those components at the position between Cylinders 4 & 5 of the Intake Camshaft “Problem Lobe”. It has been a good and productive day...moving things closer and closer to the Engine Install Date. “The FrankenOiler Machine” will go a long way towards making this happen successfully.
More to Follow...
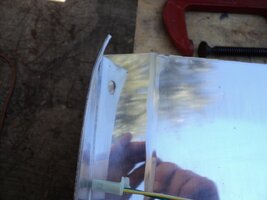
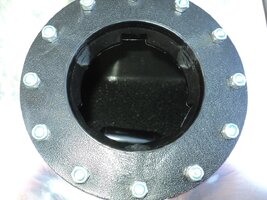
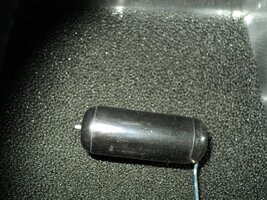
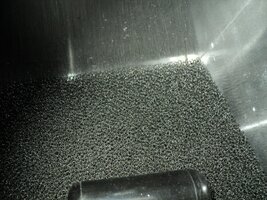

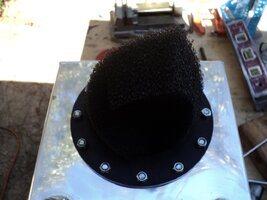

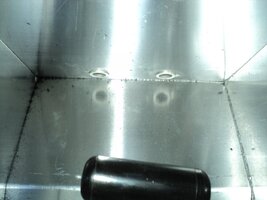
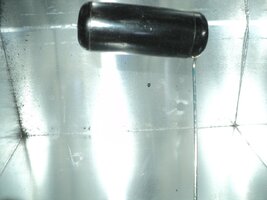
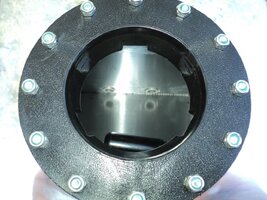
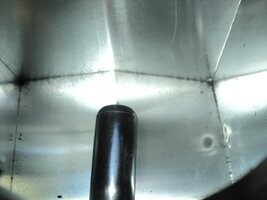
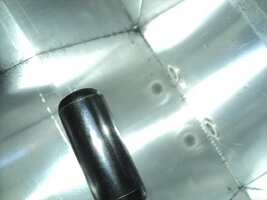


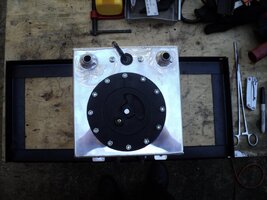
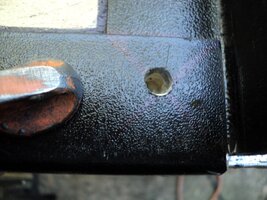
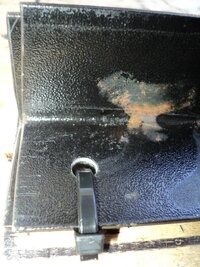
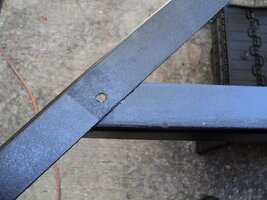

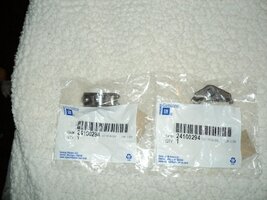
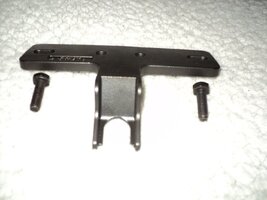
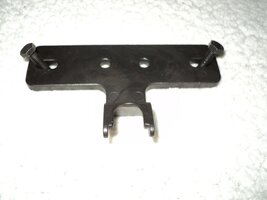

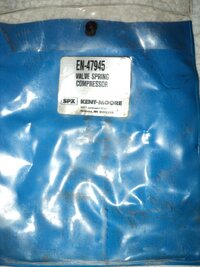
Last edited: