There is an Old Joke about a Young Man who was running pell-mell down a sidewalk in New York City, freshly shaved and adorned in a Clean Suit with a small White Rose tucked into the Button Hole of his Lapel. Suddenly, an arriving Yellow Cab pulled up slightly ahead of him at curbside and the Elderly German Gentleman Passenger inside stepped briskly out in front of this young fellow. The flushed and excited Kid blurted out,“Oh Please Sir... Can you tell me… How Can I Get To Carnegie Hall?” The Elderly Man smiled wanly and whispered with a cupped hand towards the young man…
“Practisss ...Mein Zohn… Practisss...”.
While that scenario bears a lighter and humorous tone ...when applied to continuing the work on the GM 4.2L LL8 Engine Block this evening… the idea behind it is a very serious one. Prior to committing to Bolting up all of the TIME-SERT Hardware and performing this “Surgical Thread-Line Upgrade”… I think it it worth mentioning that before using any such arcane equipment ...it will be very important for anyone intent upon performing this Machine Shop Level Quality of work… is to Practice and Get Familiar With The TIME-SERT Techniques on Something Comparable to the Engine Block Set Up… First:
To that end… I've ordered several inexpensive Solid Aluminum Blocks that bear substantial bulk and material large enough to allow me to simply Copy Over the Dimensions of the Mains Bolt Holes from the Aluminum Buttresses inside the Engine Block and then Drill Out and Tap those Holes to include the upper Dowel Cylinder area and the submerged section with the M10X1.50X24.5MM Bolt Hole SERT. Using a Sacrificial Practice Block of Aluminum will make this possible. Then I’ll photo-document all of these Machining Prep Procedures and post them back here before actually performing the Final, Real Job on the (14) Mains Holes in the Upper Engine Block:
2"X 2" 6061 SQUARE ALUMINUM SOLID FLAT BAR 6" long +.25"/-0 T6511 New Mill Stock
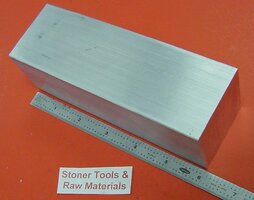
https://www.amazon.com/gp/product/B01F80WLJY?pf_rd_p=c2945051-950f-485c-b4df-15aac5223b10&pf_rd_r=8XHWHKGQYB7ZVJP67FEK
My reasons for making this effort serves three purposes:
(1) I want to Show How These Steps Get Accomplished for those with serious interest in the procedures.
(2) I want to Practice and Hone the Skills I’ve already acquired using THE TIME-SERT SYSTEM:
(3) If any Mistakes Can Be Made... You will want them to happen on the Sacrificial Aluminum Block.
I did a preliminary set up of all these Bits & Baubles... and photo-documented how all of this stuff should look look when properly placed for the purposes of TOOL ALIGNMENTS. These images show that the required TIME-SERT Hardware includes the Modified Base Plate-Alignment Bracket, The Bolt Hold-Down Stand-Off, The Knurled Metric Pin Guide, The Knurled Metric Alignment Pin... and last but not least… The Zinc-Plated 10.9 (Grade 8) M10X1.50X70MM Hold-Down Bracket Bolt. Click on the Link to my latest “Flickr-Bucket” to view/download those images:
https://www.flickr.com/photos/126111508@N07

“Practisss ...Mein Zohn… Practisss...”.
While that scenario bears a lighter and humorous tone ...when applied to continuing the work on the GM 4.2L LL8 Engine Block this evening… the idea behind it is a very serious one. Prior to committing to Bolting up all of the TIME-SERT Hardware and performing this “Surgical Thread-Line Upgrade”… I think it it worth mentioning that before using any such arcane equipment ...it will be very important for anyone intent upon performing this Machine Shop Level Quality of work… is to Practice and Get Familiar With The TIME-SERT Techniques on Something Comparable to the Engine Block Set Up… First:
To that end… I've ordered several inexpensive Solid Aluminum Blocks that bear substantial bulk and material large enough to allow me to simply Copy Over the Dimensions of the Mains Bolt Holes from the Aluminum Buttresses inside the Engine Block and then Drill Out and Tap those Holes to include the upper Dowel Cylinder area and the submerged section with the M10X1.50X24.5MM Bolt Hole SERT. Using a Sacrificial Practice Block of Aluminum will make this possible. Then I’ll photo-document all of these Machining Prep Procedures and post them back here before actually performing the Final, Real Job on the (14) Mains Holes in the Upper Engine Block:
2"X 2" 6061 SQUARE ALUMINUM SOLID FLAT BAR 6" long +.25"/-0 T6511 New Mill Stock
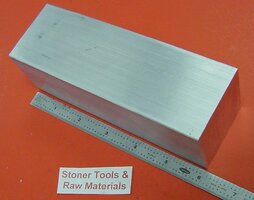
https://www.amazon.com/gp/product/B01F80WLJY?pf_rd_p=c2945051-950f-485c-b4df-15aac5223b10&pf_rd_r=8XHWHKGQYB7ZVJP67FEK
My reasons for making this effort serves three purposes:
(1) I want to Show How These Steps Get Accomplished for those with serious interest in the procedures.
(2) I want to Practice and Hone the Skills I’ve already acquired using THE TIME-SERT SYSTEM:
(3) If any Mistakes Can Be Made... You will want them to happen on the Sacrificial Aluminum Block.
I did a preliminary set up of all these Bits & Baubles... and photo-documented how all of this stuff should look look when properly placed for the purposes of TOOL ALIGNMENTS. These images show that the required TIME-SERT Hardware includes the Modified Base Plate-Alignment Bracket, The Bolt Hold-Down Stand-Off, The Knurled Metric Pin Guide, The Knurled Metric Alignment Pin... and last but not least… The Zinc-Plated 10.9 (Grade 8) M10X1.50X70MM Hold-Down Bracket Bolt. Click on the Link to my latest “Flickr-Bucket” to view/download those images:
https://www.flickr.com/photos/126111508@N07

Last edited: