Two strange things happened.
First: I left the ignition in the RUN position over night (somehow I made a dumb mistake

.) By morning the battery had discharged to 3 volts.
I discovered the dead battery ONLY AFTER something else interesting happened.
Second: After watching videos about disassembling the fuse box, I learned that there's smaller blocks of connectors enclosed in the box.

eyebrowhuh:Then a bell went off.) Back when I was a new owner, I unscrewed these bolts thinking that they would release the fuse box cover (the one that snaps on and off.)
I never re-tightened this bolt (or the others.) This bolt draws the lower connection block tight up against it's contacts. My theory: Over time the lower block of connections that this bolt secures, worked lose, and the fuel pump circuit opened.
With the bolts re-tightened, I measured 0.4 ohms of resistance to ground through the pump circuit. (fuel pump relay w/pigtails bottom center)
Voltage across the relay from constant power to the pump circuit is 12.89 volts. At this point I expected the TB to fire right up,,,and it did.
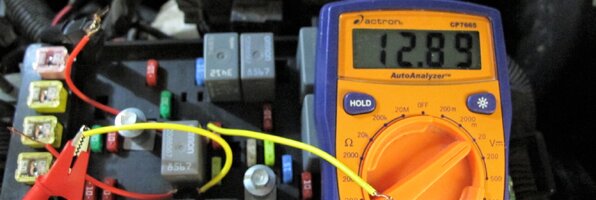