Hiya FloMaxSS, thanks for explaining some of your design and constructions. I appreciate hearing your thoughts on how to approach some of the design issues and potential impacts on weight.
Having read your ideas, I believe I will continue with my current plan. You mentioned you were fitting modern battery technology, but didn't mention the cost. My project has definite spending limits, so if I use some salvaged wire and a $30 used battery out of a wrecked Honda at the wrecking yard, I'm good! I may regret some of my choices later, but for now I will follow my ideas.
Responding to your post, I will add an update to the progress report.
The assembly of the fuel system is underway. Thanks to
@limequat for assisting me in selecting the right bits for solving some of the details in an affordable manner. I'll be using the early model fuel rail with integral regulator. Those are 90* adapters to 6 and 8AN fittings attached to the rail.
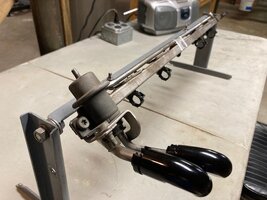
The fuel injectors I'll use are 80lb Deka units, and will be direct fit with the connector form that matches the later injectors, seen on the left.
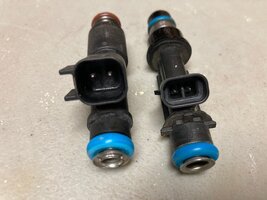
I have the fuel tank assembly prepared, with a Walbro pump and generic filler with out/in line fittings. The blue fitting is a roll over check valve.
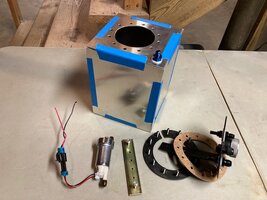
Here it is mocked up. It is 640 cubic inches or 2.77 gallons in capacity. Less the pump of course!
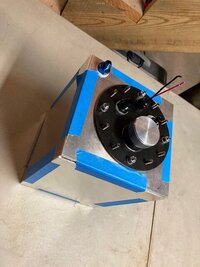
With another acknowledgement to
@limequat I have been purchasing the pieces needed for the electrical system, so at the moment I'm waiting for my credit card to cool down a bit before I purchase the injectors and PTFE fuel and vent hose.
Meanwhile, I thought I would assemble an IC water box, since I have the metal and wish to maximize air density to for realizing the maximum benefit of burning ethanol fuel.
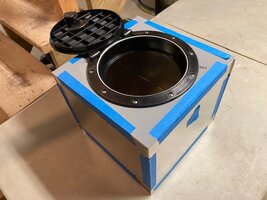
I have contemplated the IC pump delivery and return details, but this system is not a priority. I can add the hose and vent bungs to the tank after the tank is welded. In the short term I will start by running the car at atmospheric temperatures by welding a MAF bung onto an inlet pipe.
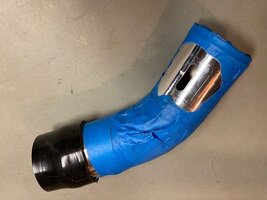
Another project I'm working on is to assemble another wire loom for the test platform, since the race car engine retained the first one I built. This is good indoor work for when it's cold and/or wet outside.
I did have to disassemble my outdoor hoist for concrete repair. The concrete cracked under the column. Tightnening the anchor bolts did not solve the issue and the column was too loose for me to trust. I'm making this project a priority because I have a couple of small jobs that will produce income for my race car budget.
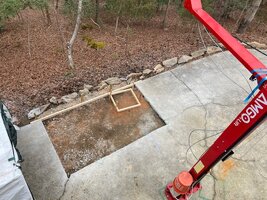
That is my February update, with more to come as I discover more time and money.
Thanks fellas, I hope you are all doing well. Please comment and let me know your thoughts.
Rick